Silicone enhances the reliability of automotive electronics
It is estimated that 85% of all automotive application innovations today are related to electrical and/or electronic. As electromechanical is gradually replacing traditional mechanical and hydraulic functions, as well as consumer demand for new value-added electronic functions, some experts believe that the electronic technology value of each vehicle can reach an average of 40% soon, and ten years ago people still Think this is impossible. Unfortunately, the failure rate due to electrical/electronic faults is also on the rise, prompting oem and Tier 1 suppliers to adopt demanding reliability standards, which has led many manufacturers to seek new materials and designs that change this trend.
This article refers to the address: http://
Heat (especially when high humidity and other adverse environmental conditions also exist) often leads to component failure. When the temperature fluctuates widely (in the most common case in automotive applications), joints and components experience fatigue caused by thermal expansion and contraction, resulting in mechanical failure. Metal dendrites can grow in a compact space between circuit board traces, ultimately resulting in short circuits and component failure. It has also been found that the reliability and lifetime of semiconductor devices depend on the junction temperature, and a temperature reduction of 10-15 °c can increase component lifetime by a factor of two.
Traditional material chemistry
Traditional electronic equipment materials are used to improve the reliability of automotive electronics, including a wide range of chemical materials and applications. The materials are typically epoxy, urethane, polyisobutylene (pib), para-xylene and acrylic, each with its own unique advantages and limitations. Applications include bonding
Agents, sealants, conformal coatings, gels, potting agents and thermal materials.
Epoxy materials are often bonded to different substrates. They can be cured at room temperature or under heating. However, if they are used in high temperature environments for a long time, their performance will be limited. Epoxy resins are generally hard and opaque and provide good abrasion, moisture and chemical resistance. Like other hard coatings, epoxy resins do not reduce the stress caused by varying degrees of thermal expansion between components, circuits, and substrates. In fact, they can cause extreme stresses between extreme temperatures or thermal cycling.
Polyurethane rubber can also be bonded to different common substrates to provide a wide range of softness (low modulus) in the cured material. Although they provide good resistance to abrasion, chemicals, and oils, they often require the use of a primer to achieve good bond strength to the metal. Polyurethane rubber formulations typically exhibit low moisture permeability and good low temperature flexibility with the ability to reduce stress. Most urethane rubbers have limited high temperature properties, and they are difficult to cope with in these high temperature environments, especially in high humidity environments, and are not easy to repair.
Similar to urethane rubber, polyisobutylene formulations can be bonded to different substrates to provide a wide range of flexibility when cured, while also providing good low temperature performance, but relatively resistant to solvents, oils, fuels and chemicals. difference.
Paraxylene is used in conformal coating synthesis due to its very uniform coating, good penetration characteristics and excellent stitch coverage. However, its shortcomings include relatively high cost, sensitivity to contaminants, easy cracking during vibration, and the need to apply this material in a vacuum, which limits its use.
Acrylic materials have good adhesion to different substrates and can be cured at room temperature or accelerated under heat. They have excellent low moisture absorption, good handleability and fast drying, but they have significant drawbacks in terms of heat and hydrolytic stability. Typical solvent-based formulations cure to hard, wear-resistant solids, and acrylics are often considered a low-cost option, but their competitiveness is declining based on changing specifications and safety considerations for solvent use. Due to its hardness, acrylic acid lacks the ability to reduce the stress caused by expansion and contraction in thermal shock.
Silicone material
In the electronics industry, silicones are often used as a general term for different polymeric materials, and most commercial silicone formulations are based on the pdms (polydimethylsiloxane) molecular formula. Electronic component manufacturers offer silicone formulations in the form of adhesives, sealants, potting compounds, gels, conformal coatings, thermal management materials, and even component packaging materials and semiconductor coatings. In addition, silicon is the basic material of silicone. Pure silicon is a semiconductor metal and is the main material for most active semiconductor components.
Silicone chemistry offers a range of different protective materials, including tough, friction-resistant elastoplastic coatings and soft, stress-relieving elastomers. Board manufacturers can choose from a range of room temperature curing (rtv) materials (temperature-cured materials can accelerate at medium temperatures) or specify solvent-free heat-curing formulations for high-speed processing. The performance of silicones enables automotive electronics components to have higher reliability and longer life. These properties include: thermal stability, elasticity, moisture resistance, adhesion to common substrates, low ionic impurities, and compatibility with processing techniques.
One of the most useful properties of silicone materials when used for electronic applications for the first time 30 years ago was the stable dielectric properties over a wide range of temperatures and frequencies. The intermolecular forces of silicone polymers change very little with time (even under wide temperature fluctuations), so physical and electrical properties are very stable.
Another important factor in improving component reliability is moisture resistance. Silicone hydrophobicity means that they do not readily absorb water molecules. At the same time, high gas permeability allows moisture to escape quickly, eliminating potential sources of corrosion. In addition, pdms' very low surface tension and excellent wetting characteristics, as well as the bonding properties obtained with advanced viscous enhancers, help achieve void-free bonding, further improving overall reliability.
Low modulus is also important to minimize stress on the electronic components because the elastomeric material can help reduce vibrational effects and absorb differences in thermal expansion that can damage sensitive components and substrates. In the typical operating temperature range of automotive electronics, current silicone formulations do not exhibit glass temperature (tg), so the modulus remains fairly constant during this cycle. This performance is significantly different from the elastic epoxy used for electronics. The modulus of the elastomeric epoxy adds more than three orders of magnitude between the extreme high and low temperatures often encountered in automotive applications.
.
Cured silicones are chemically inert and extremely stable. Many products operate while the temperature is within the range of 250 ° C (-50 ° c ~ + 200 ° c), and can maintain their physical properties. This makes silicone one of the chemical materials that can withstand harsh environments (the harsh environment in which automotive electronics must work).
application
Adhesives/sealants are primarily used to bond components in electronic modules or to encapsulate enclosures to isolate dust, water or other impurities. The main advantage of silicone adhesives is their potential to increase reliability through unique flexibility and stress relief. When the components and boards shrink due to rapid thermal cycling expansion, the elastomeric silicone binder helps absorb thermal expansion and avoids stresses transmitted from the rigid adhesive to the assembly. Their unique thermal stability allows them to remain elastic under extreme temperatures and repeated thermal shocks.
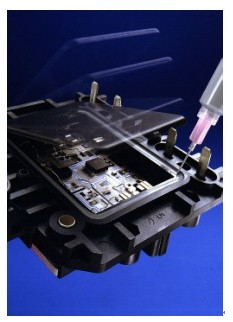
Figure 1: Silicone adhesives are used for wafer sticking, component sticking, cap sealing and other demanding applications to withstand extreme temperatures and contamination in extreme operating environments.
Specification makers often look for binders with the highest tensile strength after curing, but this material is usually hard and less ductile and therefore does not cause thermal expansion. Thermal cycling
During or after prolonged use, elevated stresses on the surface of the circuit can damage components or connections, resulting in equipment failure.
In automotive electronics applications, it is better to use materials with good adhesion that maintain their performance over a long period of time in a variety of environments. Due to its low modulus after curing, silicone adhesives are very effective in eliminating thermal and mechanical stresses, which significantly enhances reliability and service life.
Certain applications or processes have uniquely high requirements that require the use of unique properties of the binder. For example, some silicones are designed to cure at low temperatures, which is especially useful for heat sensitive components and substrates. In other applications, it is suitable for quality control acceptance to verify that the material is applied correctly before moving to the next production step. In these cases, silicone binders are often designed in conjunction with UV dyes to allow the sensor or camera control system to verify that the necessary coverage is achieved. Special intermediates can also be used to synthesize silicone binders with extremely low volatility, some of which have a volatile content low enough to be classified as an aviation grade material.
When there is a heat dissipation problem, the use of a thermally conductive filler can significantly enhance the thermal conductivity of the silicone adhesive. Thermally conductive silicone adhesives are designed to help eliminate heat from components and circuits, resulting in higher reliability and longer life in components in the engine compartment at high temperatures.
Silicones can utilize two distinct bonding mechanisms: mechanical and chemical. Mechanical bonding is a physical bond that depends on surface roughness, wetting and penetration. Surface cleanliness is important for mechanical bonding. The substrate must be relatively free of impurities, plasticizers and oils. Chemical bonding is carried out by the reaction between the catalytic binder and the substrate.
Silicone binders offer a wide range of processability and a wide range of curing conditions. Many products can be cured at room temperature. Heating accelerates the curing of some products. Some formulations are easy to adjust viscosity, allowing manufacturers to use the same binders at high speed, high heat production lines and temperature sensitive components that cannot withstand high temperatures. Another advantage in certain applications is the specific flow properties, whether the assembly requires retention of a high viscosity paste or a flowable self-leveling adhesive that fills the voids and irregular channels.
Conformal coatings are used on thin layers on circuit boards and parts to increase environmental and mechanical protection and significantly extend service life. Silicone conformal coatings protect components and circuits from moisture and impurities, helping to avoid shorting and corrosion of conductors and solder joints. They also protect sensitive components and circuits from solvents and scratches.
In general, silicone coatings offer an extremely wide range of temperature fluctuations, good stability and moisture resistance, diverse processability, low toxicity and ease of repair. Like their binder competitors, silicone conformal coatings are both hard, scratch-resistant solids and a soft, flexible material that allows the user to choose the formulation that best suits the particular application.
One of the key factors in the use of conformal coatings to protect circuits is their ability to achieve complete surface coverage of all good adhesions. The very low surface tension of the silicone and excellent wetting characteristics help achieve a void-free bond that provides overall reliability by not allowing any moisture condensation. Silicone gas permeability means that moisture below any coating can be dissipated and moisture in liquid form can be removed.
Application of electronic components in the engine compartment often requires conformal coatings to be more flexible to avoid unnecessary stress on the pitch and very small components. The difference in coefficient of thermal expansion (cte) between hard conformal coatings, substrates, and components can actually damage small pins and joints, especially under repeated temperature cycling conditions. This causes the coating to be damaged and used as a protected substrate. Elastomeric silicone coatings help reduce wire damage and circuit damage caused by thermal cycling, resulting in higher reliability and lower quality issues.
Traditionally, coatings, impregnation, injection or flow coating applications have increasingly used silicones for selective coating and automated coating operations, enabling high speed automated processing. Some formulations are designed for room temperature or heat accelerated curing, while others are specifically developed for high speed, high temperature processing.
Figure 2: Low-viscosity silicone conformal coating applied to assembled circuit boards. Its ability to adjust viscosity without solvent allows low viscosity silicone conformal coatings to be applied to a wide range of components, protection requirements and processing equipment.
[photo courtesy of nordson asymtek corp. ]
The potting agent is a protective material designed to be fully implanted with electronic components and circuitry. They are especially designed to isolate the circuit from very harsh environments and provide high voltage insulation for high voltage circuits to protect the connectors from thermal and mechanical stresses. Silicone potting agents are commonly used for thick layers.
A growing number of silicone potting agents have self-adhesive properties which, when cured to above 100 ° C, are well bonded to many common substrates. Other materials require a primer to achieve complete bonding. Testing (or accelerated testing) close to actual use conditions is critical to predict long-term performance in any application.
Like most silicone products, potting agents offer a variety of options. They have high shear strength, optical clarity, flame retardancy or extreme low temperature properties. Specific materials provide thermal conductivity or volatility, while other materials are used to meet ul specifications.
Silicone potting agents are typically supplied in the form of a solvent-free two-component liquid with a mixing ratio of 1:1 (based on curing agent). Some formulations are designed to have a ratio of 10:1. When mixed in the proper proportions, they cure into a resilient, stress-free elastomer. Some materials rooms are warm
It can be cured, while other materials require heat to cure. Silicone potting agents typically have minimal shrinkage and they do not release heat (exothermic curves) or harmful by-products. They are cured even when they are completely sealed, regardless of their thickness.
Insulating gels are special grades of potting agents that cure to very soft materials with good cushioning, elasticity and self-healing properties. Colloids provide the best way to relieve thermal and mechanical stress while maintaining elastomer volume stability. They are used in particular for thick layers to completely seal a denser structure, especially high density leads. Special materials are used to improve performance such as high optical penetration, solvent and oil resistance, low volatility or flame retardancy.
The main characteristic of gel materials is that they have a tacky surface after curing, which allows them to maintain physical adhesion to most substrates without the need for a primer. This tack allows the silicone to self-repair when the cured adhesive is damaged or cut to effectively reseal the assembly. This self-healing capability also allows for direct circuit testing of the probes through the gel without sacrificing material protection. Many other materials may not have the same attributes that allow rework or repair.
Like other silicone materials, gels also have good wetting properties and are in intimate contact with the substrate and components, minimizing microscopic voids that collect moisture. The solidified gel easily excludes liquid water and allows moisture from the surrounding environment to penetrate. Since there is no chance of accumulating in voids or covered surfaces, moisture in the air does not have any negative effects.
The organosilica body is a solvent-free formulation and is usually supplied as a two-component, low-viscosity liquid with a mixing ratio of 1:1. However, it can also be provided as a one-component material, thus eliminating the need for metering and mixing. Two-component materials can be cured at room temperature or mildly, while one-component materials require heat curing without the risk of heat or by-products. Some gels are designed for extremely fast UV curing for high speed machining. As with many silicone materials, certain impurities that prevent curing can affect gel cure. The best results are obtained using a common substrate cleaner such as vms (volatile methyl siloxane), isopropanol, toluene or acetone.
Figure 3: Two-component silicone gels can be mixed in a special mixer to provide a 1:1 ratio. This is confirmed by the uniform green color that appears after mixing the blue and yellow components.
As smaller engine compartments and energy-consuming components drive engineers to focus on innovative technologies that remove excess heat, automotive control unit manufacturers are increasingly focusing on thermal interface materials. Tim (thermal interface material) is a thermally conductive channel between a heat source and other surfaces or media such as heat sinks or ambient air. Recognizing that tim is an important source of thermal resistance in electronic design, researchers are increasingly emphasizing the potential of these materials to improve heat dissipation.
An important feature of any tim is its ability to be in intimate contact with the substrate, which reduces air voids and aids in heat transfer. Due to the excellent surface contact of the silicone material and the void-free coverage of the substrate, tim often chooses silicone materials. Silicone materials have been found to have excellent stability in thermal management applications and to retain their physical properties more permanently than exposed to the same conditions.
Silicone tim can be produced in a variety of physical forms, including thermal conductive adhesives, void fillers, gels, potting agents, preformed sheets, and even phase change materials from solid to non-flow paste at specific temperatures. Similar to other silicone materials, silicone tim low modulus means that they are elastic enough to absorb the difference in coefficient of thermal expansion (cte) without transferring stress to the component or substrate.
Thermal management materials can be used for special conditions including low volatility, flame retardancy, low bond thickness or other requirements. Because of its multiple physical states, silicone tim can meet the requirements of different applications.
trend
The organic binders and protective materials used in many automotive electronics markets cannot withstand the higher heats that new designs cause. Higher reliability requirements also exceed the limits of traditional products used to produce components and boards. Higher temperatures also exacerbate the mismatch in thermal expansion coefficient (cte), increasing stress on the component surface, causing bending, physical damage, and premature failure.
In current and emerging automotive designs, higher temperatures in the engine compartment and increased electronic component power (especially in electromechanical applications or hev (hybrid electric vehicle) control units) have led to the need for higher heat resistance. In addition, optically clear silicones are rapidly entering the automotive market, which is increasingly evident in the fact that they are a key factor in the stability protection of light-emitting diodes and forming optical instruments and optical sensors.
Due to its physical properties and widely used processing properties, silicones will soon become the initiators of automotive electronics. By improving the performance and reducing the failure of electronic and optical circuits and components, silicone materials are designed to meet the automotive industry's need for safer, lighter, higher performance components – with higher reliability than ever – and can gradually Application in harsh environments.
FGI`s FGSVG series Static Synchronous Compensator (STATCOM) can enhance power transmission capacity, reduce power loss, compensate reactive power, control harmonics, suppress flicker, stabilize grid voltage, balance three-phase system, change system damping characteristics and improve system stability. FGI`s STATCOM series products can be widely used in petrochemical, power systems, metallurgy, electrified railways, urban construction and other industries.
Static Synchronous Compensator
Static Synchronous Compensator,Abb Static Var Compensator,Static Series Compensator,Static Series Compensator,Statcom Project,Statcom ABB
FGI SCIENCE AND TECHNOLOGY CO., LTD , https://www.fgi-tech.com